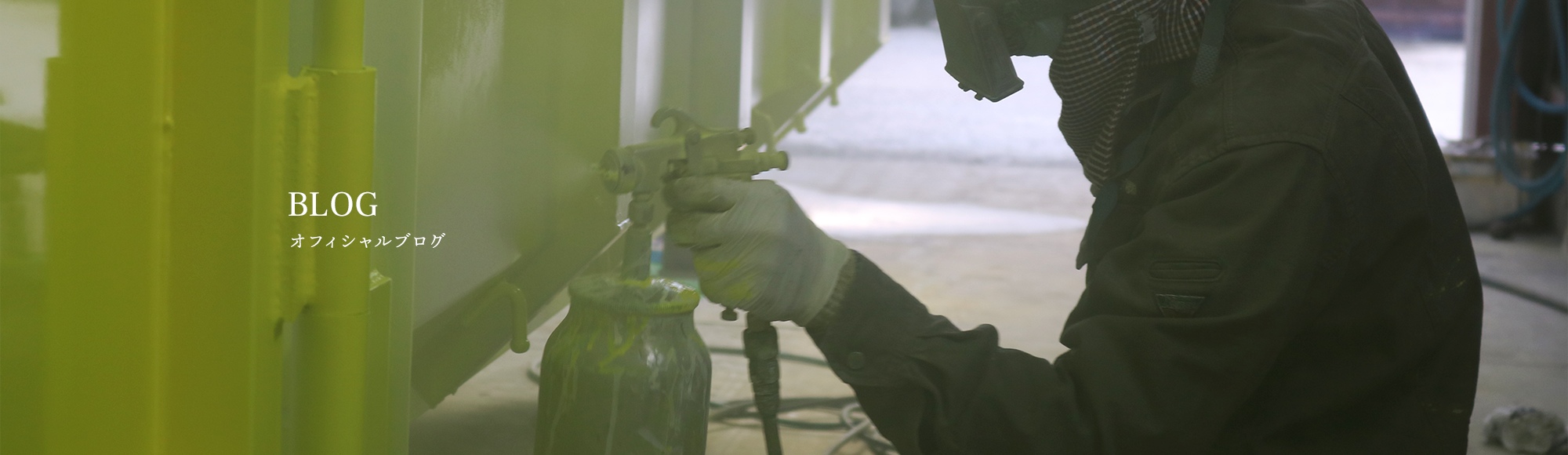
皆さんこんにちは!
ネクストステージ株式会社、更新担当の中西です。
さて今回は
~確認事項~
ということで、コンテナ製造における事前確認事項を、工程別に深く掘り下げてご紹介します!
コンテナは、物流や建設、災害対策、さらには住宅・店舗など多用途で利用される重要なインフラ資材です。その耐久性・密閉性・加工精度が、輸送効率や安全性、顧客満足に直結します。
そのため、製造現場では作業開始前の「事前確認」が製品品質を左右する決定的要素となります。
コンテナ製造は、次のような工程で構成されます:
設計・仕様の決定
材料の手配と受け入れ検査
加工・溶接・組立
塗装・表面処理
検査・出荷
それぞれの工程の前に適切な事前確認を行うことで、不良品・工程遅延・安全事故のリスクを大幅に減らすことができます。
最初の段階で「設計ミス」や「仕様の不明確さ」があると、製造工程に大きな支障が出ます。
クライアントとの使用目的・荷重・耐候性の確認
国際規格(ISO, CSC)や業界基準への準拠状況
搭載設備(電気設備、換気、断熱材など)の有無と仕様
積載物に応じた床強度・錆防止処理の要否
ドアの種類(シングル・ダブル・ロールアップ等)や開閉方向
特注仕様(窓付き、内装付き、冷凍機付など)の図面化
👉 Point: CAD図面とチェックリストを使い、**顧客承認済みの「最終仕様書」**を元に製造することが原則です。
製造に使用する鋼材やパネル、金具などは、全体品質の基礎となります。
仕入段階の確認を怠ると、後工程で致命的なトラブルに繋がります。
材料の鋼種(SS400、SUS304等)と板厚
溶接性・防錆性の確認(亜鉛メッキ有無など)
規格サイズ・数量・寸法公差のチェック
ロット番号・ミルシート(材料証明書)の確認
変形・キズ・錆の有無
👉 Point: 材料のロット管理はトレーサビリティに直結するため、受入検査記録を残すことが重要です。
この工程では、ミス=不良製品直結です。作業前の段取りが品質と効率を大きく左右します。
使用する治具・工具の点検(溶接機、クレーン、トーチなど)
組立図面・溶接指示書の確認と現場共有
作業者の資格(溶接技能者、フォークリフト運転者など)確認
防火・防災対策の確認(消火器、スパッタシート、避難経路など)
搬送計画・作業順序の確認(レイアウト設計)
👉 Point: 特に溶接の順序と歪み制御は品質に直結するため、事前シミュレーションや試作品による検証が推奨されます。
コンテナは過酷な環境に置かれるため、塗装の密着性と耐久性が求められます。
前工程のバリ取り・脱脂・錆除去の完了確認
使用塗料の種類・カラーコード(顧客指定色含む)
吹付け装置の圧力・吐出量・ノズル確認
塗布量(膜厚)の指定と計測方法の確認
作業環境(湿度、気温、通風)の適正化
👉 Point: 塗装の不良(ピンホール、たれ、未着色)は再作業が大変なため、養生・乾燥工程も含めて工程管理を徹底しましょう。
最後の検査と確認を怠ると、すべての工程が水の泡になります。
寸法・対角長の誤差確認(JIS/ISO準拠)
ドア開閉確認(ロック、パッキン、気密性)
床荷重試験や防水テストの実施
錆や塗装のはがれの有無
シリアル番号・製造ラベルの貼付確認
梱包・出荷形態の最終チェック(運搬中の損傷防止)
👉 Point: 検査結果は記録化し、品質保証書(出荷検査票)として顧客に提出する体制を整えると、信頼性が大幅に向上します。
コンテナ製造は、長年の経験と熟練技術がものを言う世界ですが、
見落としや伝達ミスが大きなロスや不具合に直結することもまた事実です。
だからこそ、各工程の「事前確認」をルール化・チェックリスト化することで、品質・納期・コストを安定的に管理できます。
工程 | 確認内容 |
---|---|
設計 | 使用用途・荷重・仕様の承認・図面確認 |
材料 | 鋼種・寸法・ミルシート・損傷有無 |
加工 | 工具点検・作業手順・安全管理 |
塗装 | 脱脂処理・塗料種類・膜厚管理 |
検査 | 寸法・密閉性・塗装外観・最終表示 |